
等離子體清洗及其應用
微電子工業中的清洗是一個很廣的概念,包括任何與去除污染物有關的工藝。通常是指在不破壞材料表面特性及電特性的前提下,有效地清除殘留在材料上的微塵、金屬離子及有機物雜質。目前已廣泛應用的物理化學清洗方法,大致可分為兩類:濕法清洗和干法清洗。
濕法清洗在現階段的微電子清洗工藝中還占據主導地位。但是從對環境的影響、原材料的消耗及未來發展上看,干法清洗要明顯優于濕法清洗。
干法清洗中發展較快、優勢明顯的是等離子體清洗,等離子體清洗已逐步在半導體制造、微電子封裝、精密機械等行業開始普遍應用。
2等離子體清洗
2.1等離子體清洗的機理
等離子體是部分電離的氣體,是物質常見的固體、液體、氣態以外的第四態。等離子體由電子、離子、自由基、光子以及其他中性粒子組成。由于等離子體中的電子、離子和自由基等活性粒子的存在,其本身很容易與固體表面發生反應。
圖1簡單描述了等離子體清洗的機理,主要是依靠等離子體中活性粒子的“活化作用”達到去除物體表面污漬的目的。就反應機理來看,等離子體清洗通常包括以下過程:無機氣體被激發為等離子態;氣相物質被吸附在固體表面;被吸附基團與固體表面分子反應生成產物分子;產物分子解析形成氣相;反應殘余物脫離表面。
等離子體清洗技術的最大特點是不分處理對象的基材類型,均可進行處理,對金屬、半導體、氧化物和大多數高分子材料,如聚丙烯、聚脂、聚酰亞胺、聚氯乙烷、環氧、甚至聚四氟乙烯等都能很好地處理,并可實現整體和局部以及復雜結構的清洗。
等離子體清洗還具有以下幾個特點:容易采用數控技術,自動化程度高;具有高精度的控制裝置,時間控制的精度很高;正確的等離子體清洗不會在表面產生損傷層,表面質量得到保證;由于是在真空中進行,不污染環境,保證清洗表面不被二次污染。
2.2等離子體清洗分類
2.2.1反應類型分類
等離子體與固體表面發生反應可以分為物理反應(離子轟擊)和化學反應。物理反應機制是活性粒子轟擊待清洗表面,使污染物脫離表面最終被真空泵吸走;化學反應機制是各種活性的粒子和污染物反應生成易揮發性的物質,再由真空泵吸走揮發性的物質。
以物理反應為主的等離子體清洗,也叫做濺射腐蝕(SPE)或離子銑(IM),其優點在于本身不發生化學反應,清潔表面不會留下任何的氧化物,可以保持被清洗物的化學純凈性,腐蝕作用各向異性;缺點就是對表面產生了很大的損害,會產生很大的熱效應,對被清洗表面的各種不同物質選擇性差,腐蝕速度較低。以化學反應為主的等離子體清洗的優點是清洗速度較高、選擇性好、對清除有機污染物比較有效,缺點是會在表面產生氧化物。和物理反應相比較,化學反應的缺點不易克服。并且兩種反應機制對表面微觀形貌造成的影響有顯著不同,物理反應能夠使表面在分子級范圍內變得更加“粗糙”,從而改變表面的粘接特性。還有一種等離子體清洗是表面反應機制中物理反應和化學反應都起重要作用,即反應離子腐蝕或反應離子束腐蝕,兩種清洗可以互相促進,離子轟擊使被清洗表面產生損傷削弱其化學鍵或者形成原子態,容易吸收反應劑,離子碰撞使被清洗物加熱,使之更容易產生反應;其效果是既有較好的選擇性、清洗率、均勻性,又有較好的方向性。
典型的等離子體物理清洗工藝是氬氣等離子體清洗。氬氣本身是惰性氣體,等離子體的氬氣不和表面發生反應,而是通過離子轟擊使表面清潔。典型的等離子體化學清洗工藝是氧氣等離子體清洗。通過等離子體產生的氧自由基非常活潑,容易與碳氫化合物發生反應,產生二氧化碳、一氧化碳和水等易揮發物,從而去除表面的污染物。
2.2.2激發頻率分類
等離子態的密度和激發頻率有如下關系:
nc=1.2425×108v2
其中nc為等離子態密度(cm-3),v為激發頻率(Hz)。激發頻率與等離子態密度。
常用的等離子體激發頻率有三種:激發頻率為40kHz的等離子體為超聲等離子體,13.56MHz的等離子體為射頻等離子體,2.45GHz的等離子體為微波等離子體。
不同等離子體產生的自偏壓不一樣,如圖3所示[2]。超聲等離子體的自偏壓為1000V左右,射頻等離子體的自偏壓為250V左右,微波等離子體的自偏壓很低,只有幾十伏,而且三種等離子體的機制不同。超聲等離子體發生的反應為物理反應,射頻等離子體發生的反應既有物理反應又有化學反應,微波等離子體發生的反應為化學反應。超聲等離子體清洗對被清潔表面產生的影響最大,因而實際半導體生產應用中大多采用射頻等離子體清洗和微波等離子體清洗。
3在封裝工藝中的應用
在微電子封裝的生產過程中,由于指印、助焊劑、各種交叉污染、自然氧化等,器件和材料表面會形成各種沾污,包括有機物、環氧樹脂、光刻膠、焊料、金屬鹽等。這些沾污會明顯地影響封裝生產過程中的相關工藝質量。使用等離子體清洗可以很容易清除掉生產過程中所形成的這些分子水平的污染,保證工件表面原子與即將附著材料的原子之間緊密接觸,從而有效地提高引線鍵合強度,改善芯片粘接質量,減少封裝漏氣率,提高元器件的性能、成品率和可靠性。國內某單位在鋁絲鍵合前采用等離子體清洗后,鍵合成品率提高10%,鍵合強度一致性也有提高。
在微電子封裝中,等離子體清洗工藝的選擇取決于后續工藝對材料表面的要求、材料表面的原有特征、化學組成以及污染物的性質等。通常應用于等離子體清洗的氣體有氬氣、氧氣、氫氣、四氟化碳及其混合氣體等。表1列出了等離子體清洗工藝的選擇及應用。
3.1等離子體清洗鋁鍵合區
集成電路鍵合區的質量對微電子器件的可靠性起到非常重要的作用。封裝作為器件和電子系統之間的唯一連接,鍵合區必須無污染物和具有良好的鍵合特性。污染物(如氧化物和有機殘渣)會嚴重削弱鍵合區的粘接性能,而傳統的濕法清洗對鍵合區的污染物去除不徹底或者不能去除。研究表明,采用等離子體清洗能夠有效去除鍵合區的表面沾污物,提高鍵合區的粘接性。
Y.F.Chong在研究中采用Ar/H2(激發頻率為13.56MHz)等離子體清洗鍵合區[3]。等離子態氣體和污染物反應生成揮發性的氣體(如 CO2和H2O),然后由真空系統吸走這些氣體。清洗后采用俄歇電子能譜(AES)、X光電子能譜(XPS)和掃描電子顯微鏡(SEM)對鍵合區表面進行檢測,檢測結果表明氧化物沾污的含量大大降低,但是對鍵合區周圍的鈍化層也造成了很大的損傷。
研究結果表明[3],等離子體清洗5min后,可以觀察到鋁鍵合區表面的形態有了徹底的變化。表面上結晶結構的逐步變化隨著等離子體清洗時間增加,鍵合區的可粘接性有了很大的提高。這是由于粘接性是取決于表面結晶結構的密度和高度。據推測這些結晶結構都是由氟化物組成的,氟來源于上游CF4/O2等離子體刻蝕鈍化層的工藝。這些結晶結構通過阻止金屬間化合物的形成來削弱鍵合區和金絲連接時的粘接性。延長清洗時間的負面效應是,Si3N4鈍化層的晶粒呈現出針狀和纖維狀,而完好鈍化層的晶粒是平滑的大晶粒。圖4所示的是在Ar/H2等離子體清洗過程中,鍵合區表面氧原子濃度的變化。經過1min的清洗,氧的含量有了顯著的下降,2~5min清洗后氧的變化平緩。氧含量的下降表明了在清洗過程中有許多氧化物和氧氟化物從鍵合區表面濺射出來。氧含量的下降也表明了鍵合區的粘接性增強了。
3.2等離子體清洗對基板焊盤的影響
引線鍵合是基板和芯片之間的主要連接方式之一,在微電子封裝中,基板和芯片之間有大量的引線鍵合。除了引線絲質量、超聲能量、時間、壓力和溫度對引線鍵合產生影響外,基板上焊盤的表面特性對其也有重要的影響。基板焊盤上的污染物(如氧化物和碳氫化合物)會降低表面質量和明顯地降低引線鍵合的成功率,彌散于空間中的污染含量達到1g/m3就會極大地影響引線鍵合的強度。因此在引線鍵合前清洗焊盤表面是十分重要的。
現有的一些研究采用兩種不同機制的等離子體清洗和不同的過程參數,對清洗前后的樣品進行對比[4]。對焊盤進行表面清洗后,把接觸角作為衡量表面質量的一個重要標準;采用焊球剪切力測試和引線拉力測試來評價等離子體清洗的效果;采用俄歇電子能譜(AES)對焊盤進行進一步分析。
接觸角方法廣泛應用于衡量表面的浸潤特性,接觸角小于90°的表面是浸潤表面,大于90°的表面是不浸潤表面。具有較高表面能的固體是親水的,表面是浸潤表面;反之,具有較低表面能的固體表面是不浸潤表面。大多數有機污染物是憎水的,所以可以采用測量接觸角作為衡量焊盤表面清潔度的方法。研究表明,未進行過等離子清洗的樣品接觸角為68°;表面進行過化學反應機制等離子體清洗的樣品的接觸角為17°左右;而表面進行過物理反應機制等離子體清洗過的樣品的接觸角為28°[4]。可知化學反應機制等離子體清洗的樣品表面更加清潔一些。
焊球剪切力測試是評價焊球鍵合最直接的方法。研究表明,經過化學反應機制清洗(Ar/H2,激發頻率為2.45GHz)的樣品具有最大的焊球剪切強度。值得注意的是,經過物理反應機制等離子體清洗的焊盤的焊球剪切強度比未經過清洗的焊盤的強度要低。出現這種現象的原因是在清洗過程中濺射粒子再沉積在焊盤表面造成了“二次污染”。
J.M.Nowful等人研究了物理反應機制等離子體清洗中的再沉積現象,對經過清洗但未引線鍵合的焊盤表面進行俄歇電子能譜(AES)分析。分析結果表明,經過等離子體清洗的樣品都能夠有效地去除有機污染物。但是在經過物理反應機制等離子體清洗的樣品中,發現了新的污染物如Ag和Cu,這些元素是由從其他位置濺射出來的粒子沉積在焊盤表面形成的,從而降低了引線鍵合強度[4]。
3.3等離子體清洗銅引線框架
引線框架封裝仍是目前封裝的主流,銅合金由于具有良好的導熱性能、電性能、加工性能以及較低的價格被用作主要的引線框架材料。但是銅的氧化物和其他的一些污染物會造成模塑料與銅引線框架分層,降低器件的可靠性,進而影響到芯片粘接和引線鍵合的質量。因此保持引線框架的清潔是保證封裝可靠性重要的一步。
研究表明[5],采用氫氬混合氣體(激發頻率為13.56MHz),能夠有效地去除引線框架金屬層上的污染物。在清洗過程中氫等離子體能夠去除氧化物,而氬通過離子化能夠促進氫等離子體數量的增加。
為了對比清洗效果,J.H.Hsieh把銅引線框架在175℃氧化后進行等離子體清洗,采用兩種氣體Ar和Ar/H2(1:4),清洗時間分別為 2.5min和12min。檢測結果表明,引線框架經過清洗后表面氧化物殘余量很少。經過氬氫混合氣體清洗后的引線框架氧的含量為0.1at%,經過氬清洗的引線框架氧的含量為0.3at%。
試驗結果表明,氧化時間的增長會降低拉力。氧化物厚度的增長也會降低引線鍵合區上鍵合絲的拉力。當引線框架經過預氧化和等離子體清洗后,拉力得到了大幅度的提高,尤其是經過Ar等離子體清洗2.5min的樣品提高更加明顯。上述結果的一個可能的解釋是,氬等離子體濺射增加了表面的微小粗糙度,從而使機械性能增強和增大了化學反應的表面積。可用原子力顯微鏡(AFM)觀察表明的形貌和微粗糙度。經過氬等離子體清洗,短時間清洗后表面非常明顯地變粗糙了,長時間的清洗后表面變得光滑。而采用氬氫等離子體清洗,表面的形貌不發生變化,并且時間不對其產生影響,這可以解釋為什么氬氫等離子體清洗對拉力沒有顯著的影響。
氬氫和氬等離子體清洗結果有這么大的差別是由于清洗機制的不同。當氬作為工作氣體的時候,去除氧化物主要靠表面的濺射;而氫等離子體引入了氧和氫之間的化學反應,所以表面形貌變化不大。關于氬等離子體清洗后拉力的增強另一個可能的解釋是由于殘余的氧化物的影響,如果氧化物層的厚度小于25nm時可以增強模塑料與引線框架的粘附。實驗表明薄氧化層對拉力的影響不是很大,對拉力影響最大的因素還是來源于氬離子濺射帶來的微粗糙度的增加。
3.4陶瓷封裝電鍍前等離子體清洗
陶瓷封裝中通常使用金屬漿料印制線作鍵合區、蓋板密封區。在這些材料的表面電鍍Ni、Au前采用等離子體清洗,可去掉有機物沾污,明顯提高鍍層質量。
4結論
濕法清洗雖然在現有的微電子封裝生產中占據主要地位,但是其帶來的環境以及原料消耗問題不容忽視。而作為干法清洗中最有發展潛力的等離子體清洗,則具有不分材料類型均可進行清洗、清洗質量好、對環境污染小等優點。等離子體清洗技術在微電子封裝中具有廣泛的應用,主要用于去除表面污物和表面刻蝕等,工藝的選擇取決于后序工藝對材料表面的要求、材料表面的原有特征、化學組成以及表面污染物性質。將等離子體清洗引入微電子封裝中,能夠顯著改善封裝質量和可靠性。但是采用不同的工藝,對鍵合特性、引線框架的性能等的影響有很大差異。例如,對鋁鍵合區采用氬氫等離子體清洗一段時間后,鍵合區的粘接性能有明顯提高,但是過長的時間也會對鈍化層造成損害;對焊盤采用物理反應機制等離子體清洗會造成“二次污染”,反而降低了焊盤的表面特性;對銅引線框架采用兩種不同機制的等離子清洗,拉力測試的結果有很大差異。因此,選擇合適的清洗方式和清洗時間,對提高封裝質量和可靠性是十分重要的。
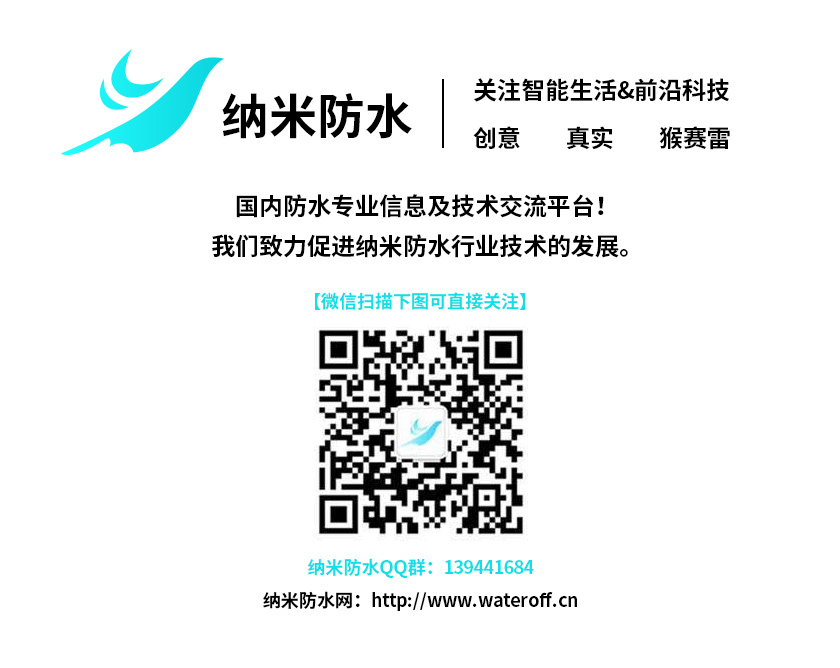
隨著電子產品防水需求的不斷提高,從原先的 IP54到現在的IP67IP68等級!市場上出現了防水透氣膜和防水透音膜,目前這兩種不同的材料應用被搞混了,今天便與大家一起討論防水透氣
最近各地降雨量激增,所以手機就難免會沾點水,作為生活中不可或缺的電子產品,防水已經成為一個十分重要重要功能,而且個人對目前的IP68手機市場是相當不滿意的。為什么?太貴
自然界中荷葉具有出淤泥而不染的典型不沾水特性(學術上稱為Cassie-Baxter狀態),具有自清潔、抗結冰、減阻、抗腐蝕等廣泛應用價值,而玫瑰花瓣則具有水滴高粘附特性(稱為Wenze
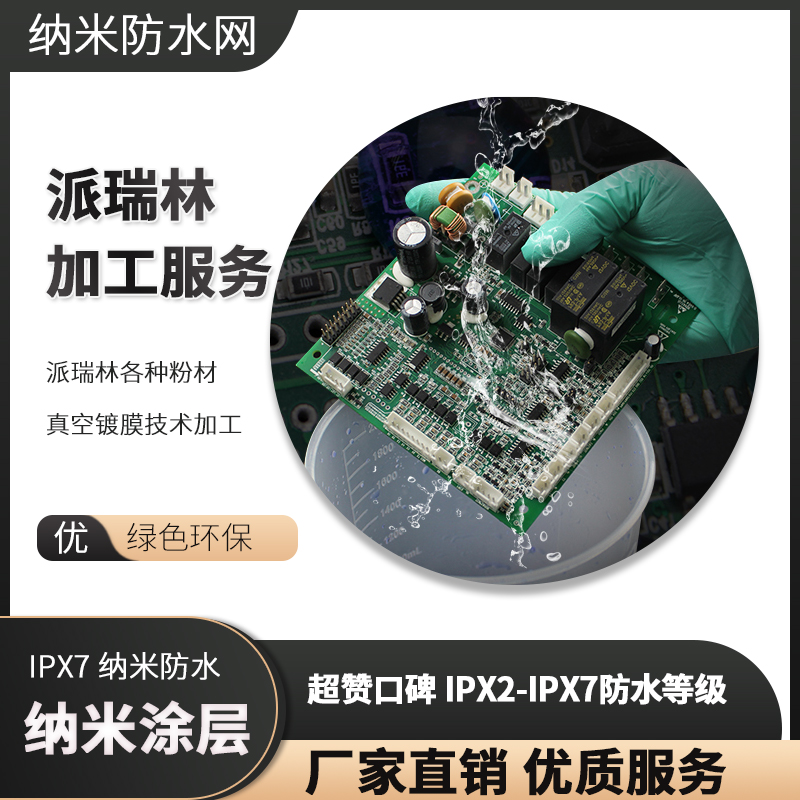
派瑞林各種粉材真空鍍膜技術加工 納米涂層防水處理
派瑞林各種粉材真空鍍膜技術加工 納米涂層防水處理
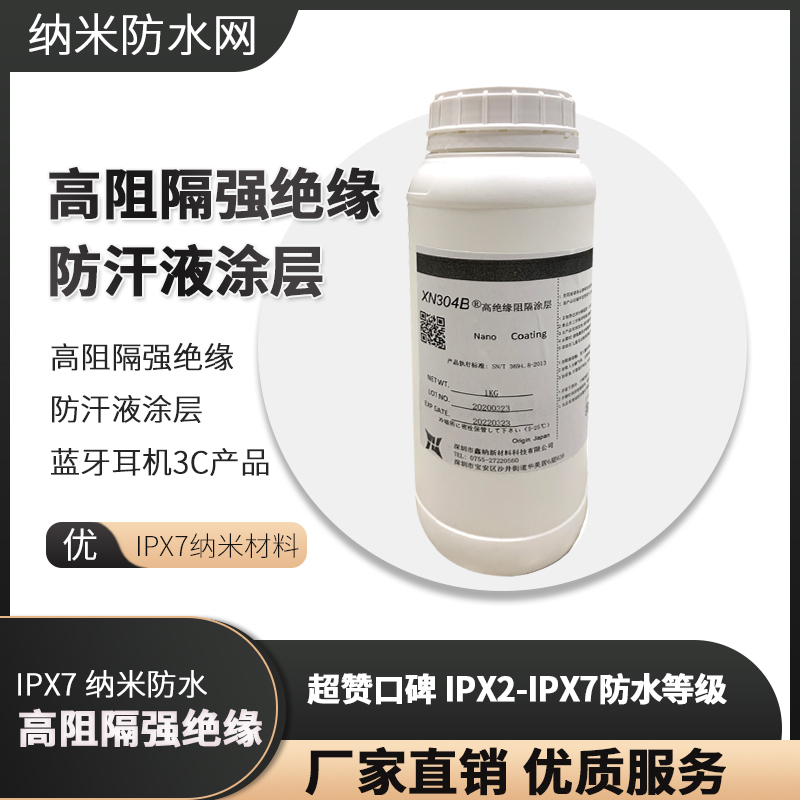
高阻隔強絕緣防汗液涂層藍牙耳機3C電子產品IPX7納米材料
高阻隔強絕緣防汗液涂層藍牙耳機3C電子產品IPX7納米材料
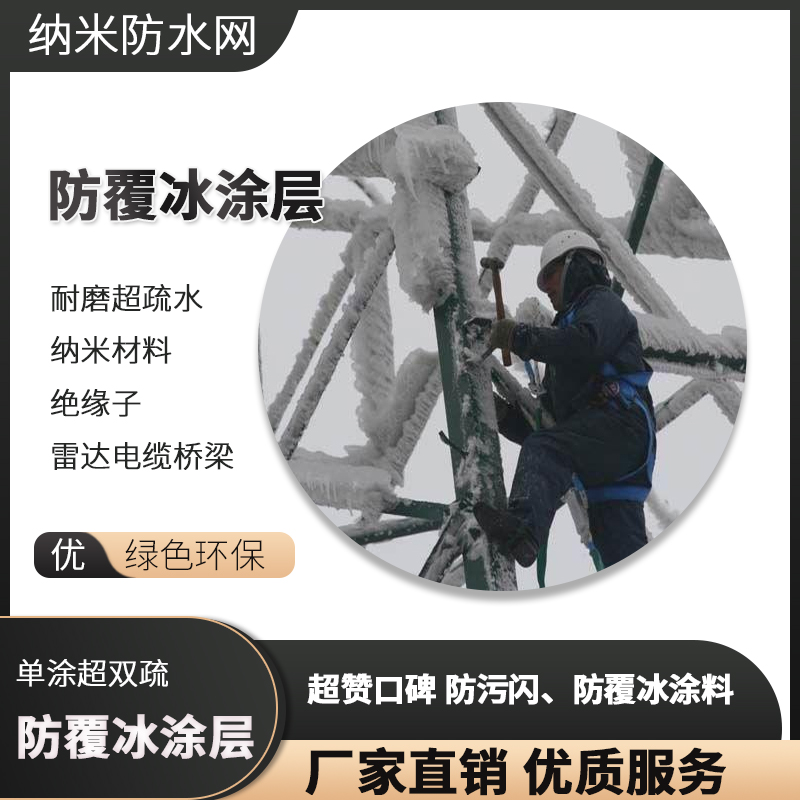
耐磨超疏水納米材料 絕緣子架空導線電纜橋梁防覆冰涂層
耐磨超疏水納米材料 絕緣子架空導線電纜橋梁防覆冰涂層
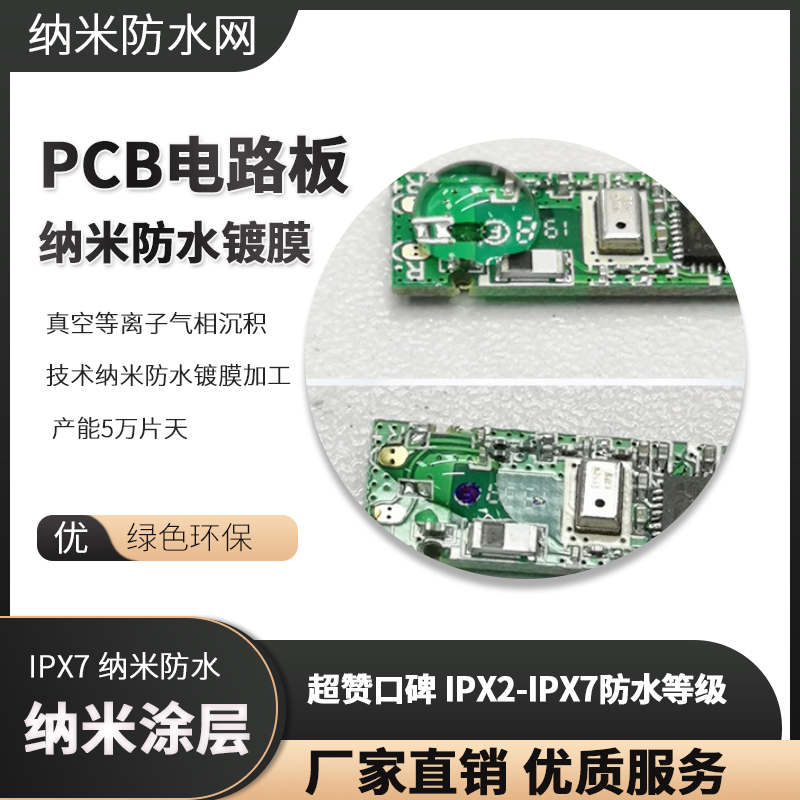
真空等離子氣相沉積技術納米防水鍍膜加工 產能5萬片天
真空等離子氣相沉積技術納米防水鍍膜加工 產能5萬片天
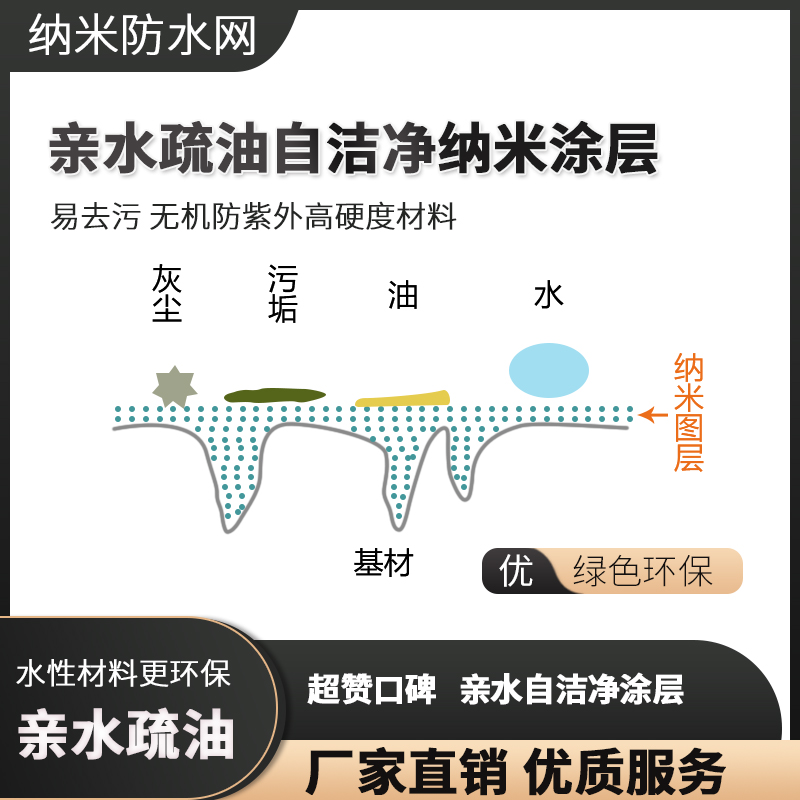
親水疏油自潔凈納米涂層 易去污 無機防紫外高硬度材料
親水疏油自潔凈納米涂層 易去污 無機防紫外高硬度材料
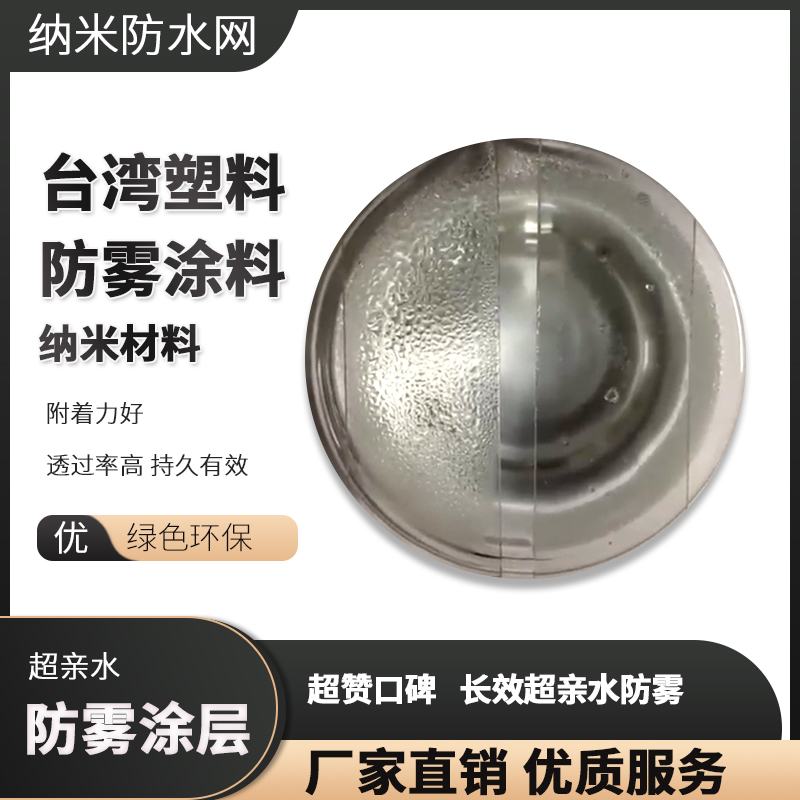
臺灣超親水防霧塑料專用 附著力好 透過率高 持久有效
臺灣超親水防霧塑料專用 附著力好 透過率高 持久有效